Liquids will take your snow operation to a major leap in the right direction to maximum efficiency and margins. An important area of discussion is methods for mechanical snow removal. By removing more of any potential ice and snowpack mechanically, you don’t have to use nearly as much liquid or salt on your post-treatment. Floating edge system plows or box plows and best practices regarding adjustment and process of plowing with a truck plow will make a world of difference in both your results and margins.
Production Rates:
We suggest setting up a network of refill silo tanks, so there is less than a 10-minute drive from the furthest customer site to a refill station. Getting this drive down to 5 minutes can provide even larger efficiency gains. The proximity of refill stations is less urgent for pre-treating as you have plenty of time to service all of your sites. Please take a look at the example below for gains on a post-treatment event.
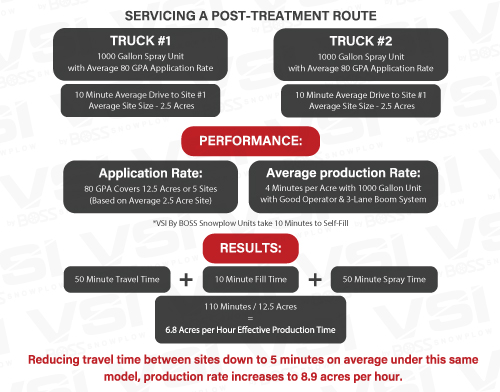
Efficient routes with localized refill points make all of the difference! Remote fill stations cost much less to set up than remote salt-loading sites. Increased production rate during storms results in needing to own fewer trucks and spray equipment to do the same amount of work; trucks and spray equipment cost a lot more than storage tanks. Refill point tanks can be refilled in the downtime between events, just like your remote salt locations would -- no skid loader and no storage container are needed. Instead, only a tank is needed with locking valves and either bollards or bunker blocks to protect it from being hit by vehicles.
Liquid Application Rates
Standard application rates are as follows:
- - 40-50 gallons per acre (GPA) for conventional pre-treat (anti-icing)
- - 60-120 gallons per acre for conventional post-treat (inter-storm or post-storm)
The more moisture that is present, the higher the application rate should be in order to be effective. The application rates can be easily and quickly changed by adjusting your automatic rate control on your spray units.
Many companies prefer to use a standard rate (80 GPA is common) for post-treatment regardless of conditions. This standard rate can sometimes become over-applied and unnecessary, especially on well “ seasoned” lots. On the contrary, in heavy snowpack or icing conditions, this standard rate could be too low for an application and will produce mediocre results. We suggest situational management to adjust your GPA rates per storm and even per site. This can be achieved quite easily when your spray systems have automatic rate control like VSI units do.
Example:
60 GPA will remove a slight glaze of snow/ice after plowing with a rubber edge pusher or truck plow. A heavy snowpack or layer of ice will require a 120 GPA to achieve the same results.
Timing & Science
Pre-treating and post-treating parking lots with liquid offers a myriad of benefits, including savings on the cost of application compared to salt and drastically better consistency in application due to simple GPS rate control systems that adjust automatically to apply the correct amount of product regardless of speed.
Applying a pre-treatment 24-48 hours before an event will provide the MOST effective results. Effective results can be seen as far out as 120 hours before an event when using an additive with your brine. Without an additive, 24 hours pre-treatment is about as far ahead as you will see impactful results especially with any rain or in high traffic or high wind areas.
The next potential step is to treat inter-storm at the first site of ice/accumulation. This treatment is to prevent anything from bonding to surfaces. A typical application rate is 60-80 GPA depending on the moisture content of the event. Preventing ice accumulation with liquids is much easier than getting rid of it once it has frozen over or accumulated.
An inter-storm treatment also provides much higher quality mechanical snow removal post-storm as there will not be a strong bond of the snow/ice with the pavement. This will translate to using less product on the final application of liquid after the plowing is complete. Stay calm if the timing does not allow for an inter-storm treatment. An increase to your final application rate to 80-100 GPA will likely meet site conditions.
Salt Purity for Brine Mixing
Most of the time when we hear about issues with slow brine mixing times, issues with the fallout, re-freeze, and plugging of spray systems it is because the quality of the salt being used to blend the brine is insufficient.
For the best and most consistent results, we must ensure at least 95% purity of your salt for optimal performance of your brine maker and spray systems. Higher purity salt can easily be sourced for brine making if your current salt is not found.